Plasma de flujo único convencional
- participación
- Tiempo de Publicación
- 2017/8/18
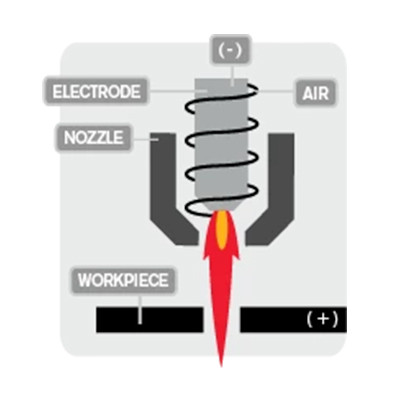
Plasma de flujo único convencional
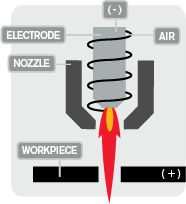
Este proceso generalmente usa un solo gas (generalmente aire o nitrógeno) que produce y enfría el plasma.
Plasma de doble flujo (sin blindaje)
Este proceso utiliza dos gases; uno para el plasma y otro como gas de protección. En sistemas más pequeños (menos de 125 amperios), el aire comprimido se usa a menudo como plasma y como gas de protección. Los sistemas sin protección de doble gas tienen una boquilla expuesta y no deben usarse para corte por arrastre.
Plasma de doble flujo (protegido)
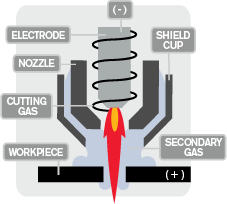
Este proceso utiliza dos gases, un gas de plasma y un gas de protección. En sistemas de menos de 125 amperios, el aire se usa a menudo como plasma y como escudo. La ventaja de la tecnología de escudo es que aísla eléctricamente la boquilla del contacto con el retroceso del metal fundido de la perforación, y también permite el corte por arrastre en aplicaciones manuales. Otras mejoras (tecnología de flujo cónico) han mejorado el rendimiento de corte y la vida útil de la boquilla en algunos sistemas .
Plasma de clase de alta definición
En este proceso, un diseño de boquilla especializado estrecha el arco y aumenta la densidad de energía. Debido a la mayor energía del arco, el plasma de alta definición logra una calidad de corte superior en materiales de hasta 50 mm (2”) con una angularidad de borde de corte superior, un corte más estrecho y velocidades de corte más altas que la tecnología de corte por plasma convencional. No es poco común con estos sistemas lograr precisiones de piezas cortadas dentro del rango de +/- 0,25 mm (0,010").
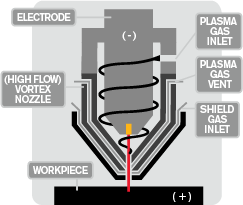
Los sistemas de alta definición actuales permiten niveles muy altos de automatización y están destinados únicamente a aplicaciones automatizadas. En los sistemas más avanzados, prácticamente toda la experiencia del operador de la máquina (necesaria para obtener una buena calidad de corte en los sistemas de plasma anteriores) se captura esencialmente en el software CAM que gestiona las operaciones de corte diarias.
Con el plasma de alta definición, los orificios cortados son redondos y prácticamente no tienen conicidad. Los bordes son cuadrados y sin escoria. Los tiempos de ciclo de corte a corte permiten niveles mucho más altos de productividad. Un sistema de plasma único puede cortar espesores de material desde un calibre delgado hasta más de 182 mm (6”), usando la misma antorcha. El soplete puede cortar y marcar la placa a través del mismo orificio de la boquilla.