Capacidad de alimentación en soldadura GMAW de aluminio
- participación
- Desde
- Internet
- Tiempo de Publicación
- 2018/8/24
Resumen
R: La capacidad de alimentación es probablemente el problema más común experimentado al pasar de la soldadura GMAW de acero a la soldadura GMAW de aluminio.
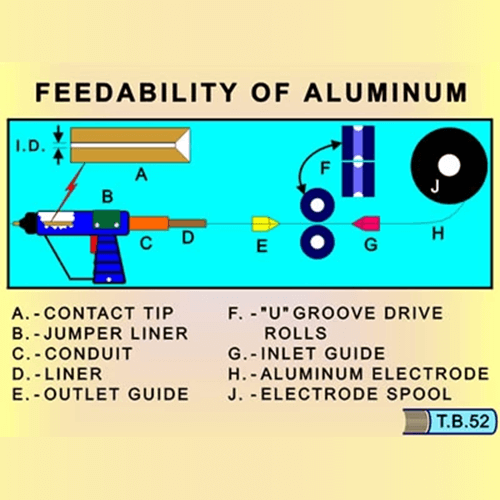
P – Recientemente pasé de la soldadura por arco metálico con gas de acero a la soldadura de aluminio con el mismo proceso. Me resulta muy difícil alimentar el alambre de aluminio a través de mi sistema de alimentación. A menudo tengo problemas con el equipo, como la fusión del alambre de soldadura de aluminio con la punta de contacto, lo que requiere la avería del sistema de alimentación y el reemplazo de la punta de contacto. Estos problemas consumen mucho tiempo y son costosos. ¿Hay alguna manera de que pueda mejorar esta situación? Estoy usando una aleación de relleno ER4043 con un diámetro de 0,035 pulgadas.
R: La capacidad de alimentación es probablemente el problema más común experimentado al pasar de la soldadura GMAW de acero a la soldadura GMAW de aluminio. La capacidad de alimentación, en este caso, se puede describir como la capacidad de alimentar de forma constante el alambre de soldadura en bobina cuando se suelda con GMAW, sin interrupción, durante el proceso de soldadura. La capacidad de alimentación es un problema mucho más importante con el aluminio que con el acero. Esto se debe principalmente a la diferencia entre las propiedades mecánicas del material. El alambre de soldadura de acero está amañado, se puede alimentar más fácilmente a una distancia mayor y puede soportar mucho más abuso mecánico en comparación con el aluminio. El aluminio es más blando, más susceptible a deformarse o rasparse durante la operación de alimentación y, en consecuencia, requiere mucha más atención al seleccionar y configurar un sistema de alimentación para soldadura GMAW. Los problemas de alimentación pueden aumentar cuando se usan alambres de menor diámetro y aleaciones de aluminio más blandas, como la 1100 y la 4043, en lugar de aleaciones más duras, como la 5356. del alambre de soldadura al interior de la punta de contacto). Para evitar problemas excesivos con la capacidad de alimentación de esta naturaleza, es importante comprender todo el sistema de alimentación y su efecto en el alambre de soldadura de aluminio. Si comenzamos con el extremo del carrete del sistema de alimentación, primero debemos considerar la configuración del freno. Se requiere que la tensión de ajuste del freno se reduzca al mínimo. Solo se requiere suficiente presión de freno para evitar que el carrete gire libremente al detener la soldadura. Cualquier presión por encima de esto aumentará el potencial de problemas de alimentación y retroceso de la quema. Se han desarrollado sistemas de frenado electrónico y combinaciones electrónicas y mecánicas para brindar más sensibilidad dentro del sistema de frenado y son particularmente útiles para mejorar la alimentación del alambre de aluminio.
Las guías de entrada y salida, así como los revestimientos, que generalmente están hechos de material metálico para soldadura de acero, deben estar hechos de un material no metálico como teflón o nailon para evitar la abrasión y el corte del alambre de aluminio.
Deben utilizarse rodillos impulsores diseñados específicamente para alimentar aluminio. Estos a menudo tienen contornos tipo U con bordes biselados y no afilados. Deben estar lisos, alineados y proporcionar la presión correcta de los rodillos impulsores. Los rodillos impulsores que tienen bordes afilados pueden raspar el alambre de aluminio blando. Estas virutas pueden acumularse dentro del sistema de alimentación y causar quemados por obstrucciones dentro del revestimiento. La presión excesiva del rodillo impulsor y/o la desalineación del rodillo impulsor pueden deformar el alambre de aluminio y aumentar el arrastre por fricción a través del revestimiento y la punta de contacto.
La identificación y la calidad de la punta de contacto son de gran importancia. Solo debe usar puntas de contacto que estén hechas específicamente para soldar alambre de aluminio, con orificios internos lisos y sin rebabas afiladas en los extremos de entrada y salida de las puntas que pueden raspar fácilmente las aleaciones de aluminio más blandas. El diámetro interior de la punta de contacto debe ser aproximadamente entre un 10 % y un 15 % mayor que el diámetro del electrodo.
La calidad del alambre de soldadura utilizado para la soldadura GMAW puede influir en las características de alimentación. Cosas tales como la suavidad de la superficie, el control del diámetro del alambre y el tratamiento final del alambre durante la operación de bobinado pueden ayudar o restar valor a la capacidad de entregar fácilmente el alambre a través del sistema de alimentación. Se deben considerar las características de calidad consistentes del alambre de soldadura de aluminio para minimizar los problemas de alimentación.
En términos de alimentación de alambre de aluminio, se utilizan cuatro sistemas de alimentación reconocidos, es decir, alimentadores de empuje, alimentadores de tracción, alimentadores de contrafase y sistemas de alimentación de carrete en pistola. Para la soldadura de aluminio, con los alimentadores de empuje y tracción, se reconocen limitaciones que dependen de la aplicación y la distancia de alimentación. Estos sistemas están generalmente limitados a una longitud práctica de alrededor de 12 pies. Con los alimentadores de empuje, el límite de la distancia de alimentación es el resultado de la flexibilidad del alambre de aluminio y su tendencia a pandearse y doblarse en el revestimiento, y con los alimentadores de tracción debido a un rápido aumento de la fricción en el revestimiento, particularmente si hay dobleces en el conducto. Los alimentadores push-pull se desarrollaron para superar los problemas de alimentación de alambre experimentados por los otros sistemas y son el método más positivo para alimentar alambre de soldadura de aluminio. Los sistemas push-pull pueden mejorar la capacidad de alimentación en muchas aplicaciones y, a menudo, son esenciales para operaciones más críticas/especializadas, como aplicaciones robóticas y automatizadas, para garantizar una capacidad de alimentación constante. El sistema de alimentación de carrete en pistola generalmente está diseñado para usar carretes de alambre de 1 libra que se montan en la pistola. Estas pistolas generalmente se enfrían con aire y generalmente se limitan a tamaños de alambre más pequeños y servicio ligero. Debido a su clasificación de corriente relativamente baja, no se adaptan perfectamente a la soldadura de producción continua de trabajo pesado, pero a menudo son bastante efectivos para la soldadura por puntos y otras aplicaciones de trabajo ligero. La elección de la
Gráfico de capacidad de alimentación